THE RECENT DEVELOPMENTS IN CERAMIC GLAZES
- Seramik Türkiye
- 25 Ağu 2020
- 41 dakikada okunur
Güncelleme tarihi: 9 Eyl 2020
Bekir KARASU, Gamze YÜKSEL and Nilperi UYSAL
Eskisehir Technical University, Faculty of Engineering, Materials Science and Engineering Department, Eskişehir
ABSTRACT
As a result of the technological developments and social expectations, in recent years the studies have intensified on the discovery of new functional glazed ceramic products improving the quality of life with the environmental consciousness. Among all the innovative ceramics those with antibacterial,antimicrobial and antifungal ability, self–cleaning efficiency, photocatalytic activity,mechanical strength, chemical endurance, lightness, anti–slip, and photoluminescence are worth mentioning. The paper aims to give general knowledge of new functional properties and then to summarize the studies recently conducted on the functional ceramic glazes.
Keywords: Ceramic glazes, Innovation, Properties, Developments.
1. INTRODUCTION
Ceramic glazes are homogeneously ground silicate mixtures that are applied onto a ceramic body surface in wet or dry form and then fired to shape a thin layer with many desired properties. Glazessupply several advantages to ceramic surfaces such as cleaning facility, increase in the chemicalresistance, strength, and surface hardness, as well as yielding an aesthetic appearance, all of which depend on the chemical composition of glaze in the first place.
There have been many changes in the ceramic industry over the years. Especially changes in processing led to a significant alteration in glaze compositions, mainly due to the shorter firing cycles, new glaze and decoration application methods, and restrictions on the use of many glaze raw materials.Changes in firing cycles, including the increased use of roller furnaces in the ceramic tile, dinnerware, and sanitaryware industries, have decreased total firing times. There is less time available to burn out organics in the body and glaze, as well as mature the body and glaze at the peak firing temperature.Changes in application like bell waterfall, airless spray, dry application, screen printing, roll printing, disc application, and inkjet printing have dictated thechanges to be made in the composition as well as the suspension of ceramic glazes. Additionally, restrictions on the use of barium, lead, cadmium, zinc, or crystalline silica have led to alterationsin glaze composition [1].
Hereby the recent innovative achievements in ceramic glazes with certain features such as antibacterial, antimicrobial and antifungal ability , self–cleaning andphotocatalytic activity, high mechanical strength and chemical durability, and photoluminescence characteristics are emphasized.
2. HISTORY OF CERAMIC GLAZES
Pottery glazing has been around for almost as long as the human race. It is unknown exactly when people first started glazing their pottery, but most archeologists agree that it was sometime between the 9th and 8th centuries BC.It is believed that the first glazes were developed around 3500 BC in Eastern Mediterranean countries by potters who tried to imitate the precious blue stone lapis lazuli. For this purpose, small beads were sculpted from steatite [Mg3Si4O10(OH)2] and then coated with azurite or malachite powders, natural ores of copper with blue and green colors, respectively. When the coated beads were fired, the coating interacted with steatite to form a thin layer of colored glass. Apart from Egypt, ancient glazes have been found in China, Mesopotamia, and Greece, each of which had developed its styled glazes according to its geography and material properties. Egyptian glazes were largely alkaline–based, as were thoseusedin China and Mesopotamia. Greek and Roman used lead–based or clay glazing. Alkali glazing is one of the oldest forms of ceramic glazing and various materials have been used in glaze contents. In Mesopotamia, ash was mixed with sand to obtain the glaze on the pottery made in that area. In Greek glazes, a mixture of soda and sand was achieved by using extra clay particles. Lead glazing was first used by the Romans from around the 1st century BC. A mixture of lead oxide and sand was placed over the pottery before it was fired [2–3].
In later periods, potters began experimenting with different combinations of crushed and ground rock powder mixed with water to coat the surface of the crocks and pots. Considering that they did not have enough knowledge of chemistry at that time, the process of developing the glaze required a long time and much effort. Over time, potters discovered mixtures that completely covered the surface of the earthenware with a waterproof glassy layer. Then they managed to produce glazes of different colors and textures by using different multiple firing cycles at different temperatures.
In the second millennium BC, lead glazes were developed in Babylon. Lead acted as a flux, which allowed the glaze to form at lower temperatures. In the 8th century BC, the Assyrians in Iran discovered another glaze additive, tin oxide. This additive yields a white opaque glaze that would completely cover the brown or reddish color of clay earthenware. Tin glazes became very popular in the Renaissance period, but their use decreased with the development of lower temperature glazes in the 1700s.
Initially, potteries were glazed to prevent the permeability of porous clay containers used for storing and transporting liquids and food. Later, thanks to the aesthetic appearance glaze provided, it started to be used as a decorative coating for the walls in the form of tiles. One of the oldest and most important examples of the use of glazed tiles in ancient Mesopotamia is the Ishtar gate (Fig. 1), built on the inner walls of Babylon during the reign of King Nebuchadnezzar II (in the 6th century BC). Blue, gold–plated and reddish tiles were used to shape both real and mythological animals [2].
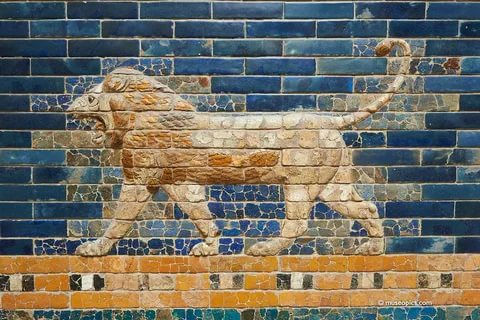
Fig. 1.Lion figure depicted in glazed tile on the Ishtar Gate (Photograph by R. Rincón, taken in the Pergamon Museum, Berlin)[2].
Over time, when potters learned to reach high temperatures, they began to develop truly permanent ceramic glazes. Thanks to the use of chemicals and minerals melting above 1100 °C in the glaze composition, the glazes fired at high temperatures became much stronger and durable. When any art museum is visited today, it is seen that the tile glazes produced in the ancient Egypt period, the Greek vases processed with red and black lined glazes, and the Chinese ceramics made of bright lead glazes and bright celadon retaining their first–day brilliance.
In the late 19th century, German Chemist Hermann Seger developed the Seger Formula, a glaze calculation method. This method, which is easier than the various formulas developed for ceramic glaze calculations, is generally employed in the industry. Seger also developed the Seger pyramid, which controls the temperature, making the firing process more accurately done. Today, studies are mainly being carried out on functional glazes.
3. INDUSTRIALLY PRODUCED GLAZES
Depending on the application being considered, conventional glazes are not fired less than 950 oC but they can be fired up to 1430 oC. Even though oxidizing are used in many cases certain products still need reduction. Glazes are employed in numerous applications, including:
Electrical porcelains
Refractories
Tiles–Wall and floor tiles
Tableware–Crockery, mugs, ceramic cups, and dinner plates
Ornaments–Figurines and giftware
Sanitaryware–Bathtubs, toilets, and basins[4–5]
Here mainly the glazes for tiles, sanitaryware (Fig. 2), and tableware(Fig. 3) will be mentioned.As a result of the technological developments and social expectations, in recent years the studies have intensified on the discovery of new functional glazed ceramic products improving the quality of life with the environmental consciousness. Especially in the tile industry, it is aimed to obtain improved durability and chemical resistance, and in the tableware and sanitaryware fields, it is targeted to develop products with antibacterial and antifungal properties and also to create more hygienic environments with less water consumption thanks to self–cleaning coatings. In addition to these, glazes with photoluminescence features are among the priority studies.
(a) (b)
(c) (d)
Fig. 2.The combination of wall and floor tiles and sanitaryware: (a)From Çanakkale Seramik of Türkiye [6], (b)Vitra Seramik of Türkiye [7],(c)Fabceramishe of Italy[8], and (d) Santa Ceramica of Russia[8].
(a) (b) (c)
(d) (e) (f)
Fig. 3.Some selected samples of tableware: (a) From Güral Porselen of Türkiye [6], (b) Porland Porselen of Türkiye [7], (c) Kütahya Porselen of Türkiye [8], (d)Jingdezhen Porcelain of China, (e)Tai Serax,and(f)Doki Japanese [8].
3.1. The Important Functional Properties for Ceramic Glazes
3.1.1. Antibacterial, Antimicrobial and Antifungal Ability
It has beenrecently demonstrated that highly reactive metal oxide nanoparticles exhibit excellent biocidal action against Gram–positive and Gram–negative bacteria. Thus, the preparation, characterization, surface modification, and functionalization of nano–sized inorganic particles open the possibility of formulation of a new generation of bactericidal materials [10].The antimicrobial activity of silver nanoparticles against yeast, Escherichia coli (E. coli) and Staphylococcus aureus (S. aureus) was investigated and it was reported that nano–sized silver particles were an effective bactericideand have great promise as antimicrobial agents in various fields such as medical devices and antimicrobial systems [11–12].Marambio–Jones and Hoek published a review paper of the antibacterial effects of silver nanomaterials, including proposed antibacterial mechanisms and possible toxicity to higher organisms. While there is some evidence that silver nanoparticles can directly damage bacteria cell membranes, they appear to exert bactericidal activity predominantly through the release of silver ions followed (individually or in combination) by increased membrane permeability, loss of the proton motive force, inducing de–energization of the cells and efflux of phosphate, leakage of cellular content, and disruption DNA replication [13]. Antibacterial Ag–doped P2O5–SiO2 monoliths were successfully prepared by sol–gel method and the porous structure was formed after heating and it was determined thatthis kind of porous monoliths has a good antibacterial property to restrain E. coli [14].
Stoneware porcelain tiles (extruded or dry pressed) have high resistance to deep abrasion, very low (0.5 %) water absorption, high hardness, and suitable resistance to thermal shock and frost. Unfortunately, such ceramic tiles do not have antimicrobial activity and microorganisms easily grow on their surfaces, particularly in hot and humid environments, which may cause problems to human health. Therefore, the creation of tiles with antimicrobial activity has significant practical and commercial importance. The most common bacteria in the wet domestic environments are S. aureus and E. coli. These are usually found on floors and walls covered with glazed ceramic tiles. At present, public health is a social concern. News about the contamination of pathogenic microorganisms in critical areas such as hospitals, slaughterhouses, restaurants, industrial facilities raise concerns in the community, so antimicrobial and antifungal materials and products are increasingly demanded by a larger market. The emergence of new generation materials that can meet this demand can maintain better environmental hygiene and safety conditions by certain ceramic products with bactericidal and fungicidal properties whose surfaces can prevent or eliminate the growth of pathogenic microorganisms. Thus, to increase the competitiveness in the ceramic industry innovative products with higher quality and high added value started to be developed. However, there is a significant increase in production costs due to the introduction of new stages in the production process. Another problem is that the antibacterial effect of the additives included in the glaze composition by additional heat– or cold–treatment is not long–lasting and the protective layer can be removed from the surfaces by the abrasion forces [15]. Seabra et al. [16] developed the porcelain stoneware tiles having an antimicrobial efficacy above 77 % for S. aureus, and 81 %, for E. coli. They reported that the antimicrobial action results from the combined effect of silver, chromium, and iron ions.
Hydrophobic surfaces are also known to have antimicrobial effects by restricting the adherence of microorganisms. However, ceramic products are produced by high temperature processes resulting in a hydrophilic surface. Özcan et al. modified an industrial ceramic wall tile glaze composition by the inclusion of metallic zinc powder in the glaze suspension applied on the pre–sintered wall tile bodies by spraying. They reported that the micro–patterned surface topography of the nanocrystalline ZnO granules imparted an antimicrobial character to the ceramic tile surfaces which werewell correlated with the hydrophobicity. The bacterial proliferation on the tiles with the zinc modified glaze was suppressed up to over 99 % [17].
Fig. 4 inhibits the antibacterial sanitaryware product of Creavit Co. of Türkiye.
Fig. 4. Sanitaryware product with antibacterial properties [18].
3.1.2. Self–Cleaning and Photocatalytic Activity
Self–cleaning surfaces possess an important place in the plastic, metal, textile, and ceramic industries, and many studies have been carried out to improve this feature. The concept of self–cleaning glass was first introduced by Watanabe et al. [19] in 1992 on titanium–coated ceramic tile. Midtdal and Jelle [20] aimed to give a comprehensive state–of–the–art review of the self–cleaning glazing products available on the market today and investigate methods for measuring the self–cleaning effect.Self–cleaning products from several manufacturers that utilize two different self–cleaning technologies of either photocatalytic hydrophilic or hydrophobic capability are presented. The photocatalytic hydrophilic products in question are self–cleaning glazing products ready–to–use when purchased, whilst the presented hydrophobic products are coatings that must be applied to existing glazing products in order to yield a water–repellent and self–cleaning surface. Fig. 5 presents the illustration of how self–cleaning glass works [20].
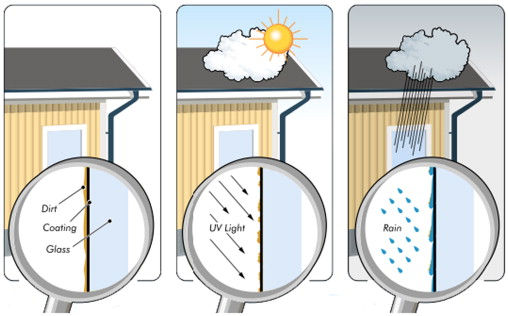
Fig. 5.Illustration of how self–cleaning glass works, in three steps, from left to right: (1) activation of the coating by UV radiation and natural dirtying, (2) decomposition of the organic dirt, and (3) rainwater washes away the loosened and degraded dirt (Pilkington Group Limited) [20].
In the self–cleaning process of a hydrophilic surface, water droplets form a thin layer on the surface. This smooth spreading plays an important role in removing dirt on the surface. It also allows the surface to dry faster and become more transparent. In other words, it prevents misting/fogging of surfaces. On hydrophobic surfaces, water droplets roll on the surface, while carrying dirt and showing self–cleaning properties [21–22]. Nanostructures can be employed to create hydrophobic surfaces, forming air gaps that prevent the contact of the surface with liquid. In this area, SiO2 [23] and CuO [24] additives are used to obtain a lotus–like effect.
Self–cleaning efficiency increases in outdoor environments where the material may be exposed to rain and water flow. In this case, the surfaces are required to have a super hydrophilic property. Thus, with the reduced water contact angle, it forms a thin water film on the surface and makes it possible to wash the impurities that do not decompose. For this reason, self–cleaning ceramic tile will perform better on super hydrophilic surfaces with a high decontamination rate. To obtain such surfaces, titanium dioxide (TiO2)is used.It decomposes organic pollutants by exhibiting photocatalytic properties and provides a hydrophilic surface to promote water distribution on the surface to complete the self–cleaning process [25].Fujishima et al. [26] reported that the best usage of self–cleaning TiO2 surfaces should be on exterior building materials because they are exposed to abundant sun exposure and natural precipitation. Although TiO2, which is employed in surface coatings under normal conditions, creates hydrophilic surfaces, hydrophobic surfaces can also be formed when TiO2 is used in nanoscale. Fig. 6 shows a ceramic washbasin with a self–cleaning glaze.

Fig. 6.Ceramic washbasin with a self–cleaning glaze by Foshan OVS Sanitaryware Ceramic Co. Ltd. of China [27].
Although increasing industrialization provides economic benefits, it also brings environmental problems with it. Today, news about diseases that arise due to environmental problems in industrial areas draw attention. One of the most sensitive issues of the European Union countries is the protection of the environment and hence human health. Therefore, the production and development of environmentally friendly products are one of the main topics that have been studied in recent years. Industrial pollution, in particular, affects both the pollution of the environment and the life of the buildings. Besides, environmental pollution causes the growth of bacteria and viruses that adversely affect human health. For this reason, it is essential to develop self–cleaning, environmentally friendly photocatalytic systems that both reduce air pollution and degrade bacteria, viruses, and toxic organic substances. Traditional ceramics do not have antibacterial or photocatalytic effects against microorganisms and organic pollutants. The presence and reproduction of these pests on ceramics are undesirable for human and environmental health [28–30].
Photocatalytic systems cause active oxygen formation when exposed to UV. Active oxygen has properties such as oxidation of organic substances on the coating surface, bacteria–killing, organic stains removal, and removal of unwanted odors in the air [31]. The cheapest and most powerful photocatalyst employed in photocatalytic reactions is TiO2 in the anatase form. Since TiO2 is a semiconductor, non–reactive, and inactive substance, it remains in the environment and ensures the cleaning process.Fig. 7 exhibits self–cleaning mechanism with a photocatalytic effect.

Fig. 7. Self–cleaning mechanism with a photocatalytic effect. Stage 1–When the surface of the tile is exposed to sunlight, it produces a thin layer of active oxygen, which reduces the static cling of dirt particles present in the atmosphere.Stage 2–The active oxygen breaks down the dirt, thusreducing its adhesion capacity/strength.Stage 3–The exceptional hydrophilic properties of tile facilitate an even distribution of water between the surface of the ceramic material and the layer of dirt; the drag of the water (H&C Tiles of Grespania Ceramica)[32].
The photocatalytic process is described by six reactions. The process begins with irradiating the semiconductors with UV light. When the semiconductor absorbs energy equal to or superior than the bandgap, an electron is transferred from the valence band to the conduction band. In TiO2→ h++ e–reaction, h+, which has great reducing power, reacts with water (moisture) to generate hydroxyl (OH), which also presents high oxidizing power. On the other hand, e– accomplishes the reduction of oxygen molecule to produce superoxide anion (O2–), which is very effective on pollutants’ degradation.The O2– reacts with H+, dissociation from water, and forms HO2. From these radicals, pollutants gases, mainly NOx, are degraded. The final product, HNO3, can be washed by rainwater[33]. Titania is one of the most widely used benchmark standard photocatalysts in the field of environmental applications. However, the large bandgap of titania and the massive recombination of photogenerated charge carriers limit its overall photocatalytic efficiency. The former can overcome by modifying the electronic band structure of titania including various strategies like coupling with a narrow bandgap semiconductor, metal ion/nonmetal ion doping, co–doping with two or more foreign ions, surface sensitization by organic dyes or metal complexes, and noble metal deposition. The latter can be corrected by changing the surface properties of titania by fluorination or sulfation or by the addition of suitable electron acceptors besides molecular oxygen in the reaction medium [34].
TiO2 has three different crystal structures which are anatase, brookite and rutile. TiO2in the anatase form is the most efficient of photocatalysts for many applications. The bandgap energy of anatase TiO2is 3.2 eV and it can be only activated by UV light. Although UV light is present in the solar spectrum it is only a very limited part. For practical applications, the photocatalytic activity of TiO2needs further improvement. Doping TiO2with transition metals or noble metals is an effective way to improve photocatalytic activity.In the literature, there are several studies thatare related to the doping effect of silver. Researches which are performed on the effect of silver dopant are focused on the change of optical and electronical properties of TiO2. Moreover, since silver itself is known as a strong anti–bacterial agent it is used as a dopant for improving anti–bacterial properties of TiO2. Doping silver can give rise to the separation of electron–hole pairs and can accelerate the formations of oxidative species. In addition to this, silver can reduce particle size which is needed for increasing surface area of TiO2 [35].
3.1.3. Mechanical Strength and ChemicalEndurance
Thanks to the glazes applied to ceramic surfaces, surface dirt and deposits can be easily cleaned. However, these surfaces that are resistant to daily environments can wear out over time and lose their surface properties when being negatively affected by high or low pH valued environment. At this stage, varying the glaze content or applying a coating on the glaze surface can be used to increase and improve the surface resistance [5]. Floor tile glazes are constantly exposed to abrasive effects, especially in public areas. Depending on factors such as traffic density and the type of abrasives in such places, high abrasion resistance is expected from floor tiles. The abrasion resistance of the glaze is one of the main factors that determines the life of ceramic coatings due to the continuous abrasive effects. This resistance is improved by increasing glaze hardness. One of the ways to increase the hardness of glaze is the use of suitable glass–ceramic systems in which the harder crystal phase or phases are developed from the glassy matrix [36].
The degree of contamination and cleaning of the glaze surfaces depend on the surface micro– and macro–roughness respective to the chemical composition of the phases. Alkaline detergent solutions typically used to clean daily living surfaces cause pitting on surfaces containing wollastonite and pseudo wollastonite. The glaze recipes prepared with diopside crystals with high abrasion properties provide abrasion resistance against acids and bases as well as surface gloss. Moreover, the sol–gel technique is a very versatile method to deposit ceramic coatings in combination with a dip–coating process. The resulting coatings are of high purity and structural homogeneity. They are mesoporous and very thin as well as with defined crystalline structure and generally presenting good adhesion to the substrate [37–42].
In general, glazes show good chemical resistance in aqueous solutions. However, depending on the composition of the glaze, solution, temperature, and other conditions, ion changes, dissolutions, and absorption reactions can occur on the glaze surface. Corrosion taking place in the glaze results in a decrease in brightness, discoloration, and leads to pitting or decomposition on the surface. The chemical resistance of glazes is often interpreted by the durability of the amorphous phase, because the crystal phases in the glaze structure are assumed to have higher durability. Generally speaking, the reaction kinetics vary depending on the glaze formulation, chemical and mineral composition, and grain size of the raw material during the firing process.
It is difficult to achieve a desired and controlled surface appearance when using raw glazes in ceramics fired at lower peak temperatures or shorter firing cycles typically applied for glazed tiles. The use of frit formulations has been recently increasing. However, raw glazes are a low–cost alternative to fast–fired and fully condensed ceramics, such as frost–resistant floors and swimming pool tiles, due to their high peak firing temperatures.
3.1.4. Photoluminescence Effect
Photoluminescence is described as the event that any material can emit light after absorbing photons. The light emission eventis called photoluminescence since it is initiated by photoexcitation. When materials are stimulated with light, their electrons reach high energy levels, and the stimulated electrons release photons to return to lower energy and more stable energy levels. At this stage when photons are released, glare/glow occurs. Photoluminescence can be divided into two classes: fluorescence and phosphorescence. In both cases,materials absorb light and emit photons with less energy and shine in dark. However, when the excitation source disappears in fluorescent materials, the light emission ends immediately. In phosphorescent ones, the light emissionoccurring after the excitation source removed can take minutes or hours.This group is generally preferred for applications where phosphorescence pigments continue to emit light when the stimulation ends. Long–lasting phosphors have been developed in the SrAl2O4: Eu2+, Dy3+ systems, which emit light in blue, green, bluish–green, and yellowish–green colors, have been developed.Photoluminescent glazes are obtained by adding photoluminescent pigments to the glaze compositions. They are applied to the ceramics, absorb visible light, and gain a glowing ability in the dark, consequently adding value to the end products. Such an ability is not only evaluated for decoration in houses and other buildings but also is used in floor coverings to prevent confusion and provides guidance in emergencies. Photoluminescent ceramics can emit light at certain wavelengths, which can restrict certain molds and diseases.Thanks to this feature, it is preferred in kitchen and sanitaryware products. They are resistant to corrosion, friction, burning, and aging[43].Figs. 8–9 present luminous ceramic mosaics and pro–environment photoluminescent ceramic tiles respectively.

(a) (b)
Fig. 8. Luminous ceramic mosaics of Foshan Miclear Ceramics Technology Co. Ltd. of China, The appearance (a) in daylight (b) in the dark [44].
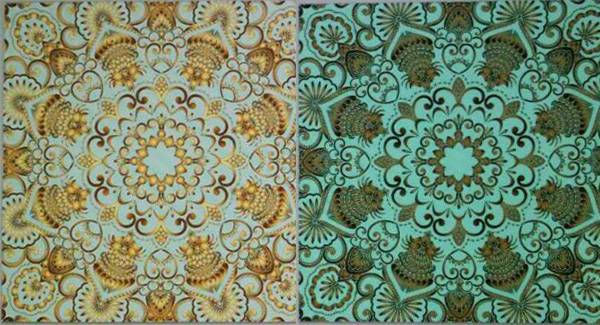
Fig. 9. Pro–environment photoluminescent ceramic tiles of Pacific Industry Co. of China, The appearance (a) in daylight (b) in the dark [45].
4. The Recent StudiesConducted on Ceramic Glazes
There have been many studies on the development of glazes with new features. Some of those made between the years 2000 and 2020 are summarized below.
Eppler conducted researches on the chemical abrasion resistance of glazes against various chemical solutions and concluded that the results depend on firing conditions as well as glaze composition [46]. Yalçın and Sevinç utilized bauxite waste in ceramic glazes [47].Karasu et al. developed and characterized zinc crystal glazes used for Amakusa–like soft porcelains [48]. Çakı and Karasu evaluated albite wastes in stoneware glazes [49].
Karasu et al. made compositional modifications to floor tile glazes opacified with zircon [50]. In another work, Karasu et al. studied the effect of albite wastes on the glaze properties and microstructure of soft porcelain zinc crystal glazes [51]. Karasu and Turan reported the effect of cobalt, copper, manganese, and titanium oxide to zinc–containing soft porcelain glazes [52–53]. Karasu et al. applied the phosphorescent glazes on bricks and roof tiles [54]. Qing et al. investigated the effect of infrared radiant powder addition on glaze development and antibacterial and antifungal activity [55].
Karasu and Tosuner microstructurally studied limonite containing satin and opaque wall tile glazes [56]. Torres and Alarcon made researches on the effect of additives on the crystallization of cordierite–based glass–ceramics as glazes for floor tiles [57].
Karasu et al. utilized the concentrator wastes of Etibor Kırka Borax Company of Türkiye in the recipe of an opaque frit used for wall tile glazes as an acid boric replacement [58], evaluated these wastes in soft porcelain opaque glazes as an alternative fluxing agent [59], investigated the effects of the red mud–based pigment addition on the physical and microstructural properties of porcelain tiles [60] and used Tunçbilek thermal power plant's fly ash in stoneware glazes as a coloring agent [61]. In the study of Vane–Tempest et al., the chemical resistance of fast–fired raw glazes in solutions containing cleaning agents, acids, or bases has been examined [62].
Karasu et al. reported the effects of red mud–based pigments on wall and floor tile glazes [63] and developed the abrasion–resistant diopside–based glazes suitable for floor tiles by compositional modifications [64]. Hupa et al. searched for the chemical resistance and cleanability of glazed surfaces [65]. Torres and Alarcón published the paper on the pyroxene–based glass–ceramicglazes for floor tiles [66], and on the effect of MgO/CaO ratio on the microstructure of cordierite–based glass–ceramic glazes for floor tiles [67]. Torres et al. investigated the effects of some additives on the development of spinel–based glass–ceramic glazes for floor–tiles [68].
Rong has a Ph.D. study on the synthesis, characterization, and biological applications of inorganic nanomaterials and determined that silver nanoparticles exhibit more antimicrobial activity than silver nitrate in the same concentration. This finding suggests that low–toxicity silver nanoparticles may be antimicrobial agents [69]. In the works of Yekta et al. floor tile glass–ceramic glaze for the improvement of glaze surface properties has been examined [70]. Torres et al. worked on the mechanism of crystallization of fast fired mullite–based glass–ceramic glazes for floor–tiles [71], and also published the paper on the effect of boron oxide on the microstructure of mullite–based glass–ceramic glazes for floor–tiles in the CaO–MgO–Al2O3–SiO2 system [72].
Agné conducted a study on the silver ion–containing glaze and concluded that sanitaryware glazes obtained by traditional methods can be scratched and damaged with abrasive cleaning agents such as powder used in the cleaning stage, and the property of the glaze may be impaired. Thanks to the easy cleaning and chemical resistance of the glazes produced by the method they developed such problems were eliminated [73]. Tulyaganov et al. worked on the influence of incorporation ZnO–containing glazes on the properties of hard porcelains [74]. Määttä et al. established the effect of different coatings on the cleanability of glazed ceramics [75], and the effects of UV–radiation on the cleanability of titanium–dioxide glazed ceramic tiles [76]. Kuisma et al. examined the effect of surface topography of different compositions and surface coatings of glazed ceramic tiles on their cleanability [77]. Increasing demands for better cleanability have led to the development of functional coatings on traditional glaze surfaces. However, the chemical and mechanical durability of these coatings is not fully understood. In the work of Kronberg et al. a traditional white sanitaryware glaze was coated with both commercial fluoropolymers and new hybrid sol–gel functional coatings [78]. Berto has written a paper dealing specifically with the possibility of using ceramic tiles as supports in which to integrate elements such as photovoltaic cells, presence sensors for detecting movement, or activating other devices, heat sensors for fire detection, electric switches, etc. Other applications already in development were also discussed, relating to the use of glaze coatings with self–cleaning, hygienic (Fig. 10), air generating, bactericidal, anti–grease, or anti–misting properties [79].

Fig. 10. Influence of the type of coating on microorganism development [79].
Sun et al. covered the glazed surface with Ag–TiO2 by liquid–phase deposition method and made sintering at 600 °C, achieving high antibacterial performance against E. coli and S. aureus bacteria [80]. Marcos et al. deposited titania layers by screen–printing in common glazed ceramic tiles [81]. Karasu et al. investigated the use of borax solid wastes in the production of fast single firing wall tile opaque glass–ceramic glazes[82].Rincón et al. developed anti–slip effect in the glass–ceramic glaze of CaO–MgO–Al2O3–SiO2system [83].
Pekkan and Karasu reported the results of their work on the production of opaque frits with low ZrO2 and ZnO contents and their industrial uses for fast single–fired wall tile glazes [84]. Thanks to the additive to the glaze composition between 0.3–0.5 % by weight, it has been observed that 99 % of the bacteria can be eliminated as a result of the antibacterial test [85]. Teixeira and Bernardin used titania polymorphs (rutile and anatase) in substitution of zirconia as the main component for producing white opacity in ceramic glazes for tile coatings [86]. Cannillo et al. examined several ceramic tiles characterized by different glazes to define the role played by the glassy and crystalline phases on the leaching mechanism and the deterioration of the mechanical properties [87]. Piispanen et al. investigated the chemical resistance and cleaning properties of coated glaze surfaces [88].
Pekkan and Karasu evaluated of borax solid wastes in the production of frits suitable for fast single–fired wall tile opaque glass–ceramic glazes [89].Yoshida et al. investigated the antimicrobial activities of porcelain glazes with antimicrobial agents made from clay minerals interlaced with silver chelate [90]. In the study of Zeng et al., Si–, P– and Zr–modified TiO2 based low temperature glazed ceramics with photocatalytic properties were prepared. Modification with Si, P, and Zr was able to effectively prevent TiO2 grains from interacting with the glaze, limiting grain growth, and preventing the transition from anatase to rutile phase. Ceramics prepared with modified TiO2 additive showed effective and durable photocatalytic properties [91]. Piispanen et al. covered the glazed surfaces by using three different methods to increase the strength of the glaze surfaces and improve their easy cleaning properties. They reported that although the fluoropolymer coating was easy to apply, its chemical and mechanical strength was poor, but the TiO2 coating showed excellent cleanability and also inhibited good results in chemical and mechanical strength [92]. Sánchez et al. published a review paper on the description of the evolution and distribution of research into porcelain tile per country, giving the major scientific and technological advances, focusing principally on the developments in raw materials compositions resulting from the introduction of certain key raw materials to enhance composition quality [93]. Melchiades et al. aimed to identify the causes of transparency loss presented by some ceramic glazes composed of frits with chemical compositions typical of optically transparent glasses [94].
Kaya et al. characterized the diopside–based glass–ceramic porcelain tile glazes containing borax solid wastes [95]. Anatase, which is the most photo catalytically active titania modification, must be stabilized to achieve a high photocatalytic activity in ceramic processes at temperatures above 1000 oC. Hofer and Penner prepared thermally stable TiO2 powders by the addition of silica and boehmite nanoparticles and deposited on corundum substrates and lead–free glazes [96].
Yeşilay and Karasu studied the process parameters determination of phosphorescent pigment added, frit–based wall tiles vetrosa decorations (Fig. 11) [97], and glass and ceramics with the phosphorescence ability [98].
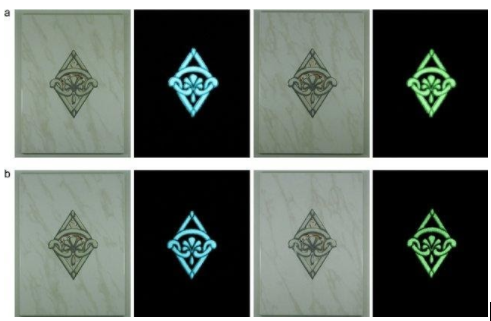
Fig. 11. The final appearances of decorated, glazed wall tiles in the daylight and the dark. Decors contain 10 % bluish–green and yellowish–green phosphorescent pigmentsand single fast–fired at 920 oC (a) and 980 oC (b) in VitrA Karo Inc. of Türkiye [97].
In the study of Gürbüz et al., to give the products antimicrobial properties, Ag–containing powder synthesis was made and added to the glaze, and environmentally friendly products were obtained by developing both photocatalytic and antibacterial functions in the same product coated with the TiO2 spray method [99]. Baheiraei et al. coated the Ag/SiO2 films on glazed ceramic tile by the sol–gel method and examined the antibacterial effectiveness of this process [100]. One of the most studied topics on functional ceramics is self–cleaning hydrophilic and photocatalytic glazes. These two features can be obtained by making additives to the glaze compositions or by coating over the glaze. Raimondo et al. worked on creating hydrophilic surfaces with a photocatalytic effect by covering the tile surfaces with TiO2. The critical point in this study is that TiO2 to be used is in the anatase phase and has a nanoscale grain size. Phase transformation of anatase and grain growth requires very tight control, especially during heat treatment [101]. Petrovič et al. examined the photocatalytic activities of coatings containing different ratios of nano TiO2 by weight on ceramic surfaces. They stated that the photocatalytic activity also increased linearly with increasing nano–TiO2 layer thickness, but nano TiO2, which is used at a ratio higher than 1 %, causes the formation of cracks on the surface [102]. Partyka and Lis reported the results of the effect of selective grinding of raw materials on the chemical resistance of ceramic glazes. Proper selection of the grain size of certain raw materials used for the production of ceramic glazes has exhibited that glazes with higher surface quality and higher chemical resistance can be obtained against the effect of both acid and alkaline solutions of a changing pH [103]. Agrawal et al. discussed the design and experimental analysis of the glaze photovoltaic thermal (PVT) tile air collector [104]. Casasola et al. have published a review article on glass–ceramics glazes for ceramic tiles [105].
Niederhousern et al. examined the effectiveness of Ag–TiO2 coatings on glazed and unglazed ceramic surfaces. It has been reported that the hydrophilic property of Ag–TiO2 coated surface increases and gives a very high antimicrobial performance [106]. Pina–Zapardiel et al. added the sepiolite with homogeneous zirconia nanoparticles distribution to a transparent ceramic glaze to study opacification, mechanical and wear resistance properties, and observed that monodispersed zircon single crystals with needle–like shape have been formed in the ceramic glaze [107]. Murugan et al. made an effort not only to demonstrate the performance of the self–cleaning coatings on building materials such as ceramic glazed tiles and glass windows but also to understand the fundamental issues that are still alive in the field of self–cleaning surfaces based on photocatalysis [108]. Zang et al. investigated the effects of tetraethyl orthosilicate modification on microstructure, crystal structure, hydrophilicity, photocatalytic activity, and stability of the film [109]. Ghosh et al worked on the glazes in the CaO–MgO–Al2O3–SiO2 system for future generation floor tiles [110].
The formulation of innovative transparent hydro repellent coatings is strongly motivated to satisfy the market request and necessity to improve the cleanability of the sanitarywares. Cacciotti et al. reported the set–up of the deposition of modified SiO2 coatings on glazed ceramic supports by spraying technique [111]. Ke et al. synthesized a photocatalytic TiO2/ZnTiO3 coating on glazed ceramic tiles by the sol–gel method and subsequent thermal treatment. The structural and morphological properties were investigated by X–ray diffraction (XRD) and scanning electron microscopy (SEM). The result reveals that the photocatalytic coating is composed of anatase TiO2 and hexagonal ZnTiO3(Fig. 12) [112]. Ghosh et al. used cordierite–based glass–ceramics to glaze floor tiles by microwave and conventional processing techniques [113].

Fig. 12. Photocatalytic degradation activity of methylene blue for a–TiO2/ZnTiO3 coating[112].
Macro–crystalline glazes containing significantly large crystals visible to the naked eye are a type of artistic glaze with a decorative and esthetic performance. The use of raw glaze compositions is a cost–effective alternative for these types of crystal glazes. Pekkan studied R2O–RO–(ZnO)–Al2O3–(TiO2)–SiO2–based raw glaze system to produce macrocrystalline glazes for Limoges porcelain bodies [114]. Tezza et al. examined the effect of sintering temperature on the photocatalytic activity of anatase ceramic glazes [115]. Solar reflective materials, so–called cool roofs, can be identified as one of the most promising solutions to counteract urban heat island. Ceramic–based products can be an excellent solution combining both good solar properties and higher durability against time, in particular, if glazed. Ferreira et al. used a traditionally engobed porcelain stoneware tile as a substrate for a new generation of colored glazes characterized by different surfaces reaching promising values in solar reflectance [116].
Mohd and Hasmaliza focused on the performance of rutile addition in glaze composition for antibacterial application [117]. Ferreira et al. aimed to propose a first overview of several ceramic glazes by analyzing their solar properties, in the perspective of creating a range of solar reflective ceramic glazed tiles [118]. Anatase is one of the common and favorable material use in the manufacturing industry due to its uniqueness and functional performances to humans and the environment. Hasmaliza et al. conducted the study focusing on the performance of anatase mixed with glaze and applied on ceramic tiles by a dip coating method [119]. Knies et al. developed a new glaze with photoactive oxides, based on the industrial ZrSiO4 glazes for sanitaryware. When ZnO was used instead of ZrSiO4, less than 20 nm surface roughness and, super hydrophilic wetting was observed under UV irradiation [120].
In the study of Gün et al., the yellowish–green phosphorescent pigment–added glazes were applied and fired at different temperatures, determining that the luminescence is better in the glaze fired at 870–880oC, and the luminescence was decreased in the temperature range of 900–910 oCas a result of pigment degradation [121]. Karasu and Çakı utilized thephosphorescent pigments prepared by dry mixing and solid–state sintering method on glazes for white earthenware body[122].Taşçi et al. developed the phosphorescent violet/purple glazes on traditional glazed tiles [123].Silva et al. prepared a 5 mole % Nb2O5 doped TiO2 solution and applied it to the glazed ceramic tile surface by spraying. They observed that the Nb2O5 additive used delayed the conversion of TiO2 from the anatase phase to the rutile phase at annealing temperatures and could prevent a decrease in the photocatalytic performance of TiO2 depending on the temperature in the production of ceramic tiles [124]. Fraga et al. reported the influence of alkali elements (Na, K) on the morphological, structural, and optoelectronic properties of CIGS ceramic tile solar cells [125]. Li et al. carried out the studies on the development of a high–reflectance ceramic tile containing titanite and the reaction sintering mechanism of the tile was confirmed. The relationship between the crystal content and reflectance was also explained [126]. In the work of Gjek et al., it was aimed to develop new compositions of white glazes without the addition of ZrSiO4 designed for sanitary products obtained in a 12–h firing cycle at a maximum temperature of 1230 °C [127]. Tarhan et al. conducted work on protecting natural resources, minimize raw material costs, and manage waste–generated pollution by reusing the vitrified sanitaryware waste products [128].
The study of Gajek et al. focused on the results of research on the development of newly designed white glazes without the addition of traditional opacifiers such as ZrO2 or ZrSiO4 intended for use in ceramic sanitary products [129]. Barrachina et al. made an investigation on the development of a glass–ceramic glaze (Fig. 13) formulated from industrial residues to improve the mechanical properties of the porcelain stoneware tiles [130]. The purpose of Li et al.’s study was to produce more excellent opaque wall tile glazes by using sapphirine instead of zirconium silicate as an opacifier. To achieve it, the chemical compositions were precisely adjusted in the system of SiO2–Al2O3–MgO–K2O–Na2O–B2O3 [131]. Cai et al. examined the feasibility of developing fast–firing opaque wall tile glazes obtained from zircon–free frits [132].Da Silva et al. overviewed the latest research on photocatalytic ceramic tiles in terms of process parameters, durability, cleanability and photoactivity, addressing challenges and solutions reported by academic and industrial sources [133]. Barmeh et al. published a paper on the influence of Ni doping on the self–cleaning properties of TiO2 thin film under visible light [134]. Terjék and Dudás aimed to determine the slipperiness of ceramic tiles and to make a comparative analysis of the different measurement methods [135].

Fig. 13. Scanning electron micrographs of the glass–ceramic glaze on a porcelain ceramic tile: a) x500, b) x5000 [130].
Reinosa et al. designed a new glaze for the ceramic tile industry with the combined layer deposition of standard glazes. It has been found that the Ca2+ and Zn2+ compounds in the glaze can complement the antimicrobial effect of up to 99.9 % [136]. Barmeh et al. coated the surface of the glazed ceramic tile with the spraying method with pure and Al–doped TiO2 coatings prepared by the sol–gel method. Al in the Al–doped TiO2 coating acted as an impurity, thereby preventing the conversion of TiO2 in the anatase form to the rutile phase, resulting in better photocatalytic performance [137].
In Selli and Yağyemez studies, they applied the photocatalytic coating containing TiO2 in the anatase phase obtained by the sol–gel method, to the surface of ceramic tiles containing Al2O3, SiO2, B2O3, CaO, MgO, ZnO, K2O, Na2O and ZrO2 [138]. VitrA Photoactive (Eczacıbaşı Vitra) tiles were covered with nano–sized titanium dioxide. Thanks to the photocatalytic properties of the coating, the self–cleaning tiles also eliminated airborne impurities and bad odors [139]. Erlus Lotus roof tiles break down organic dirt particles such as oil, soot, and moss with the help of sunlight and remove this dirt from the environment with rain. The duration of these roof tiles to remain clean is much longer than that of traditional roof tiles [140]. Another important issue for glazed products with functional properties is the resistance to chemicals and corrosion. This feature plays an important role in determining the usage area and duration of the end product. Studies on this subject have been continuing recently. Topateş et al. examined the effects of ZrSiO4, which is an important component in the glazes used in healthcare equipment, on surface properties such as opacity, roughness, hardness and bacterial effect [141]. Kronberg and Hupa examined the surface properties of the matte raw glaze containing wollastonite and diopside crystals and the chemical strength of these compositions and decided that the use of diopside–based glazes with better chemical resistance for matte glazes was more accurate, and reported that the silica content increased the chemical strength of the amorphous phases [142]. Wang et al. examined the effects of the surface properties of zirconium–containing raw glaze, zirconium–based frit glaze, double–glazed transparent glaze, and TiO2–coated raw glaze on corrosion resistance and cleanability [143]. Kunduracı et al. aimed to investigate the thermal behaviors of vitrified glazes containing phosphorescent pigment and their decoration and luminescence properties [144]. In the search of Nieves et al. the objective was to evaluate the effect of the particle size distribution of frits used to produce a transparent glaze on the glaze layer characteristics and the ink behavior (Fig. 14) [145]. Amorós et al. investigated the microstructural development and kinetics of the sintering and crystallization processes of a SiO2–Al2O3–RO (R=Ca, Mg, Sr) glass–ceramic glaze [146].
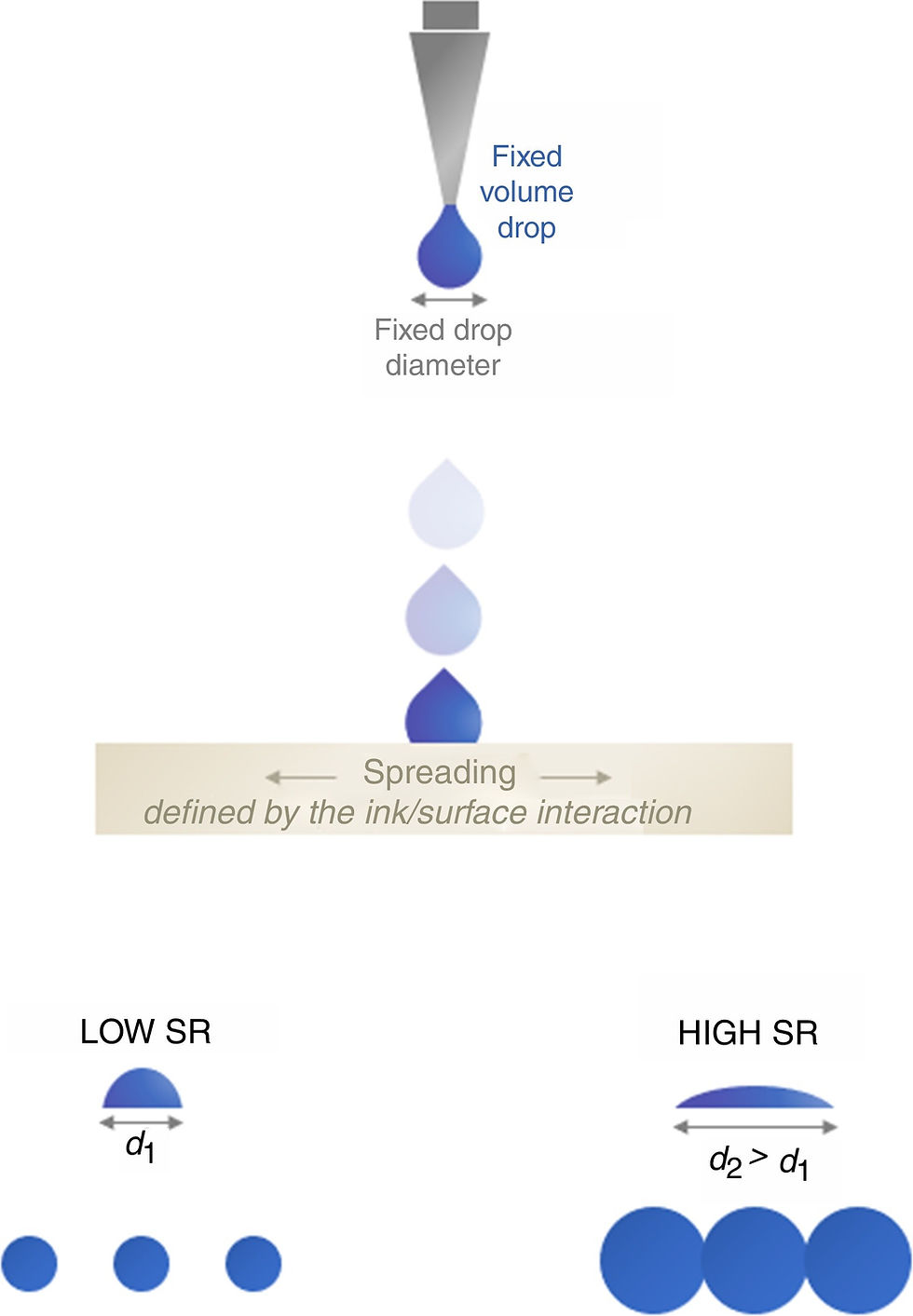
Fig. 14. Image formation: ink dots produced from fixed initial diameter drops over a ceramic surface–low and high spreading ratio (SR) [145].
5. Conclusions
Although the visuality and design of ceramic glazes are necessary to attract the customers attention, manufacturing products with functionality become more important and desired as a result of the rapid advancement of technology, taking the increasing environmental problems into an account.
With recent studies, several suitable industrial wastes have been evaluated in glaze recipes. Attempts were made to decrease glaze cost by eliminating ZrO2, ZrSiO4, and ZnO in wall tiles and sanitaryware glaze compositions. Pyroxene–, cordierite–, diopside–, mullite–, and spinel–based glass–ceramic glazes have been developed for floor tiles. Surface coatings of glazed ceramic tiles with photocatalytic and antibacterial functions have been studied in detail. Influence of several dopants (such as Ag, W, Mo, Al, Ni, and Nb) on thephotocatalytic and antibacterial activity and self–cleaning properties of TiO2 thin film was investigated. Ag/SiO2 films applied by the sol–gel method on the glazed ceramic tile was found to lead to antibacterial effectiveness. It has been reported that the photocatalytic activity increases linearly with increasing nano–TiO2 layer thickness, but nano TiO2, which is used at a ratio higher than 1 %, causes the formation of cracks on the surface. Modification with Si, P, and Zr can effectively prevent TiO2 grains from interacting with the glaze, limiting grain growth, and preventing the transition from anatase to rutile phase. The researchers conducted on the increase of phosphorescence ability of decoration glazes for wall tiles inhibited that good quality phosphorescent ceramic products are available and can be industrially produced. Solar reflective materials, so–called cool roofs, can be identified as one of the most promising solutions to counteract urban heat island. Ceramic–based products can be an excellent solution combining both good solar properties and higher durability against time, in particular, if glazed.
Consequently, new, glazed, and functionalized ceramics with the characteristics ofbactericidal, self–cleaning, photocatalytic, corrosion resistance, photoluminescence, air generating, anti–grease, anti–misting, etc.are being produced. During production energy–saving is also the focused matter. In parallel with the rapidly advancing technology and increasing demandfor new functional products, it seems that mankind will carry on getting a better quality of life.
References
[1] Barson, T., Ceramic Glazes Today, Ceramic Manufacturing Workshop and Exhibition, Lexington, 1998.
[2]Richerson, D.W., The Magic of Ceramics, The American Ceramic Society, Westerville, 2000.
[3] Priddy, B., The History of Glazing, 2017 (https://ourpastimes.com/the-history-of-glazing-12311173.html).
[4]An Introduction to Ceramic Glazes, written by AZoM, 2001 (https://www.azom.com/article.aspx?ArticleID=1020).
[5]Taylor, J. R., and Bull, A.C., Ceramics Glaze Technology, The Institute of Ceramics & Pergamon Press, Oxford, 1986.
[6]https://nuovo.com.tr/kategori/canakkale-seramik-2.html (date accessed: 16.08.2020).
[7]https://yandex.com/collections/card/5da023f9c9270d09847a775e/ (date accessed: 16.08.2020).
[8]https://yandex.com.tr/gorsel/search?text=luminous%20tiles&stype=image&lr=103835&family=yes&source=wiz (date accessed: 16.08.2020).
[9]https://yandex.com.tr/gorsel/search?p=13&text=tableware&from=tabbar&family=yes(date accessed: 17.08.2020).
[10] Stoimenov, P. K., Klinger, R. L., Marchin, G. L., and Klabunde, K. J., Metal Oxide Nanoparticles as Bactericidal Agents, Langmuir, 18 (17),6679−6686, 2002.
[11] Sondi, I., and Salopek–Sondi, B., Silver Nanoparticles as Antimicrobial Agent: A Case Study on E. Coli as a Model for Gram–Negative Bacteria, Journal of Colloid and Interface Science, 275 (1), 177–182, 2004.
[12] Kim, J. S., Kuk, E., Yu, K. N., Kim, J.–H., Park, S. J., Lee, H. J., Kim, S. H., Park, Y. K., Park, Y. H., Hwang, C.–Ys., Antimicrobial Effects of Silver Nanoparticles, Nanomedicine: Nanotechnology, Biology and Medicine, 3 (1), 95–101, 2007.
[13] Marambio–Jones, C., and Hoek, E. M., A Review of the Antibacterial Effects of Silver Nanomaterials and Potential Implications for Human Health and the Environment, Journal of Nanoparticle Research, 12 (5), 1531–1551, 2010.
[14] Liu, H., Chen, Q., Song, L., Ye, R., Lu, J., and Li, H., Ag–Doped Antibacterial Porous Materials with Slow Release of Silver Ions, Journal of Non–Crystalline Solids, 354 (12–13), 1314–1317, 2008.
[15] Noguera, J. F., Moreno, A., Gozalbo, A., Orts, M. J., Development of Ceramic Glaze Compositions with Bactericidal and Fungicidal Properties, Qualicer’10 Proceedings, Castellón Spain, 1–9, 2010.
[16] Seabra, M. P., Grave, L., Oliveira, C., Alves, A., Correia, A., Labrincha, J. A., Porcelain Stoneware Tiles with Antimicrobial Action, Ceramics International, 40, 6063−6070, 2014.
[17] Özcan, S., Açıkbaş, G., and Açıkbaş, N. Ç., Induced Superhydrophobic and Antimicrobial Character of Zinc Metal Modified Ceramic Wall Tile Surfaces, Applied Surface Science, 438, 136–146, 2018.
[18] https://www.creavit.com.tr/landing/tr/ultra-hijyen (date accessed: 28.04.2020).
[19] Watanabe, T., Hashimoto, K., Fujishima, A., In Proceedings of the First International Conference on TiO2 Photocatalytic Purification and Treatment of Water and Air, London, 1992.
[20] Midtdal, K., and Jelle, B. P., Self–Cleaning Glazing Products: A State–of–the–Art Review and Future Research Pathways, Solar Energy Materials and Solar Cells, 109, 126–141, 2013.
[21] Parkin, I. P., and Palgrave, R. G., Self–Cleaning Coatings, Journal of Materials Chemistry, 15 (17), 1689–1695, 2005.
[22] Ragesh, P., Venkatesan, A. G., Nair, S. V., Nair, S., A Review on Self–Cleaning and Multifunctional Materials, Journal of Materials Chemistry A, 2 (36), 14773–14797, 2014.
[23] Jiang, Y. D., Kitada, M., White, M., Fitz, T., and Hunt, A. T., Development of Durable Nanostructured Superhydrophobic Self–Cleaning Surfaces on Glass Substrates, Journal of Food Process Preserve, 38 (3), 1321–1329, 2014.
[24] Li, H., Yu, S. and Han, X., Fabrication of CuO Hierarchical Flower–like Structures with Biomimetic Superamphiphobic, Self–Cleaning and Corrosion Resistance Properties, Chemical Engineering Journal, 283, 1443–1454, 2016.
[25] Zhang, J., Xu, Q., Feng, Z. L., Li, M., Li, C., Importance of the Relationship between Surface Phases and Photocatalytic Activity of TiO2, Angew. Chem. Int. Ed., 47, 1766–1769, 2008.
[26] Fujishima, F., Hashimoto, K., Watanabe, T.,TiO2 Photocatalysis: Fundamentals and Applications, Tokyo Bkc, 14–21, 1999.
[27]https://yandex.com.tr/gorsel/search?family=yes&p=5&text=self%20cleaning%20ceramic%20sink&from=tabbar (date accessed: 16.08.2020).
[28] Vallée, F., Ruot, B., Bonafous, L., Guillot, L., Pimpinelli, N., Cassar, L., and André, H., Innovative Self–Cleaning and De–Polluting Facade Surfaces, In CIB World Building Congress, 2–7, 2004.
[29] Fujishima, A., Rao, T. N., and Tryk, D. A., Titanium Dioxide Photocatalysis, Journal of Photochemistry and Photobiology C: Photochemistry Reviews, 1 (1), 1–21, 2000.
[30] Benedix, R., Dehn, F., Quaas, J., and Orgass, M., Application of Titanium Dioxide Photocatalysis to Create Self–Cleaning Building Materials, Lacer, 5, 157–168, 2000.
[31] Kula, G., Karasu, B., Self–Cleaning Surfaces, Journal of Ceramic Türkiye, 108–115, 2017 (in Turkish).
[32]https://www.grespania.com/self-cleaning-ceramic-tiles/ref640013en (date accessed: 13.05.2020).
[33] Segundo, I. R., Ferreira, C., Freitas, E. F., Carneiro, J. O., Fernandes, F., Júnior, S. L., and Costa, M. F., Assessment of Photocatalytic, Superhydrophobic and Self–Cleaning Properties on Hot Mix Asphalts Coated with TiO2 and/or ZnO Aqueous Solutions, Construction and Building Materials, 166, 500–509, 2018.
[34] Kumar, S. G., and Devi, L. G., Review on Modified TiO2 Photocatalysis under UV/Visible Light: Selected Results and Related Mechanisms on Interfacial Charge Carrier Transfer Dynamics, The Journal of Physical Chemistry A, 115(46), 13211–13241, 2011.
[35] Şam, E. D., Ürgen, M. and Tepehan, F. Z., TiO2Photocatalysts, itüdergisi/dmühendislik, 6 (5–6), 81–92, 2007 (in Turkish).
[36] Albro, J. L. A., Glazes for Ceramic Wall and Floor Tiles. Evolution and Perspectives, Proceedings of Qualicer, World Congress on Ceramic Tile Quality, Castellón,Spain, 69–100, 1992.
[37] Kaya, G., Karasu, B., and Cakir, A., Characterisation of Diopside–Based Glass–Ceramic Porcelain Tile Glazes Containing Borax Solid Wastes, Journal of Ceramic Processing Research, 12 (2), 135–139, 2011.
[38] Karasu, B., Glass Ceramic Systems Suitable for Conventional Ceramic Glazes, Abstract Book of the CIMTEC 2010–12th International Ceramics Congress & 5th Forum on New Materials, Montecatini Terme, Italy, 116, 2010.
[39] Çavaç, M., Diopside Based Porcelain Ceramics, Anadolu University, Master Thesis, 2003 (in Turkish).
[40] Hocaoğlu, E., Development of Diopside–Based EngobeCompositions, Anadolu University, Master Thesis, 2004 (in Turkish).
[41] Kilerci, D. K., Investigation of Production Opportunity of Highly Resistant Floor Tile Glazes, Anadolu University, Master Thesis, 2002 (in Turkish).
[42] Brinker, C. J., Scherer, G.W., Sol–Gel Science: The Physics and Chemistry of Sol–Gel Processing, Academic Press, Inc., San Diego, CA, p. 907, 1990.
[43] Kaya, S. Y., Karasu, B., Karacaoğlu, E., General Review of Application of Phosphorescence Pigments in Ceramic Industry, the Proceedings of SERES’09 I. International, Ceramic, Glass, Porcelain Enamel, Glaze and Pigment Congress, Eskisehir, Türkiye, 608–616, 2009.
[44] https://miclear.en.ecplaza.net/(date accessed: 16.08.2020).
[45] https://pacificpigment.en.ecplaza.net/(date accessed: 16.08.2020).
[46] Eppler, R. A., and Eppler, D. R., Glazes and Glass Coatings, American Ceramic Society, 2000.
[47] Yalçın, N., Sevinç, V., Utilization of Bauxite Waste in Ceramic Glazes, Ceramics International, 26, 485–493, 2000.
[48] Karasu, B., Çakı, M. and Turan, S., The Development and Characterisation of Zinc Crystal Glazes Used for Amakusa–like Soft Porcelains, Journal of the European Ceramic Society, 20, (12), 2225–31, 2000.
[49] Çakı, M., Karasu, B., Use of Albite Wastes in Stoneware Glazes, American Ceramic Society Bulletin, 79, [10], 79–82, 2000.
[50] Karasu, B., Dölekçekiç, E., and Özdemir, B., Compositional Modifications to Floor Tile Glazes Opacified with Zircon, British Ceramic Transaction, 100 (2), 81–85, 2001.
[51] Karasu, B., Çakı, M., and Yeşilbaş, Y. G., The Effect of Albite Wastes on Glaze Properties and Microstructure of Soft Porcelain Zinc Crystal Glazes, Journal of the European Ceramic Society, 21 (8), 1131–1138, 2001.
[52] Karasu, B., Turan, S., Effect of Cobalt Oxide and Copper Oxide Additions to Zinc–Containing Soft Porcelain Glazes, American Ceramic Society Bulletin, 80 (9), 41–45, 2001.
[53] Karasu, B., Turan, S., Effects of Cobalt, Copper, Manganese and Titanium Oxide Additions on the Microstructures of Zinc Containing Soft Porcelain Glazes, Journal of the European Ceramic Society, 22 (9–10), 1447–1455, 2002.
[54] Karasu, B., Kaya, G., and Ozkara, O., Application of Phosphorescence Glazes on Bricks and Roof Tiles, 2nd International Eskisehir Terra Cotta Symposium Proceedings, 108–13, 2002.
[55] Qing, X., Wen, C., Feng, Z., Run–Zhang, Y. J., A Novel Infrared Radiant Glaze Exhibiting Antibacterial and Antifungal Functions, Journal of Wuhan University of Technology–Mater. Sci. Ed., 17,10–13, 2002.
[56] Karasu, B., Tosuner, L., The Micro–Structural Studies in Limonite Containing Satin and Opaque Wall Tile Glazes, Ceramic Forum International, DKG, 80 (9), E61–65, 2003.
[57] Torres, F. J., Alarcón, J., Effect of Additives on the Crystallization of Cordierite–Based Glass–Ceramics as Glazes for Foor Tiles, Journal of the European Ceramic Society, 23, 817–826, 2003.
[58] Karasu, B., Kaya, G., Kozulu, R., Utilisation of Concentrator Wastes of Etibor Kirka Borax Company in the Recipe of an Opaque Frit Used for Wall Tile Glazes as an Acid Boric Replacement, Euro Ceramics VIII, Key Engineering Materials, Vols. 264–68, 2505–2508, 2004.
[59] Karasu, B., Kaya, G., Karalar, M., Use of Concentrator Wastes of Etibor Kırka Borax Company in Soft Porcelain Opaque Glazes as an Alternative Fluxing Agent, Euro Ceramics VIII,Key Engineering Materials, Vols. 264–68, 2497–2500, 2004.
[60] Karasu, B., Caki, M., Akgun, E., Kaya, G., Effects of the Red Mud Based Pigment Addition on the Physical and Microstructural Properties of Porcelain Tiles, Euro Ceramics VIII,Key Engineering Materials, Vols. 264–68, 1613–1616, 2004.
[61] Karasu, B., Kaya, G., Aydasgil, A., and Kurama, H., Use of Tuncbilek Thermal Power Plant's Fly Ash in Stoneware Glazes as aColouring Agent, Euro Ceramics VIII,Key Engineering Materials, Vols. 264–68, 2501–04, 2004.
[62] Vane–Tempest, S., Kronberg, T., Fröberg, L., and Hupa, L., Chemical Resistance of Fast–Fired Raw Glazes in Solutions Containing Cleaning Agents, Acids or Bases, In Proceedings of VIII World Congress on Ceramic Tile Quality, Castellón, Spain, 155–164, 2004.
[63] Karasu, B., Akgün, E., Kaya, G., Effects of Red Mud Based Pigments on Wall and Floor Tile Glazes, Ceramic Forum International, DKG 82 (10), E 41–44, 2005.
[64] Karasu, B., Kaya, G., Gönül, A., Development of Abrasion Resistant Diopside Based Glazes Suitable for Floor Tiles by Compositional Modifıcations, 3rd Ceramic, Glass, Enamel, Glaze and Pigment Seminar with International Participation (SERES’05) Proceedings, Eskisehir, Türkiye, 615–624, 2005.
[65] Hupa, L., Bergman, R., Fröberg, L., Vane–Tempest, S., Hupa, M., Kronberg, T., Pesonen–Leionen, E., and Sjöberg, A. M., Chemical Resistance and Cleanability of Glazed Surfaces, Surface Science, 584, 113–118, 2005.
[66] Torres, F. J., Alarcón, J., Pyroxene–Based Glass–Ceramics as Glazes for Floor Tiles, Journal of the European Ceramic Society, 25, 349–355, 2005.
[67] Torres, F. J., Alarcón, J., Effect of MgO/CaO Ratio on the Microstructure of Cordierite–Based Glass–Ceramic Glazes for Floor Tiles, Ceramics International, 31, 683–690, 2005.
[68] Torres, F. J., Ruiz de Sola, E., Alarcón, J., The Effects of Some Additives on the Development of Spinel–Based Glass–Ceramic Glazes for Floor–Tiles, Journal of Non–Crystalline Solids, 351, 2453–2461, 2005.
[69] Rong, C. Synthesis, Characterization and Biological Applications of Inorganic Nanomaterials, University of Hong Kong, Ph.D. Thesis, 2006.
[70] Yekta, B. E., Alizadeh, P., Rezazadeh, L., Floor Tile Glass–Ceramic Glaze for Improvement of Glaze Surface Properties, Journal of the European Ceramic Society, 26, 3809–3812, 2006.
[71] Torres, F. J., Ruiz de Sola, E., Alarcón, J., Mechanism of Crystallisation of Fast Fired Mullite–Based Glass–Ceramic Glazes for Floor–Tiles, Journal of Non–Crystalline Solids, 352, 2159–2165, 2006.
[72] Torres, F. J., Ruiz de Sola, E., Alarcón, J., Effect of Boron Oxide on the Microstructure ofMullite–Based Glass–Ceramic Glazes for Floor–Tiles in the CaO–MgO–Al2O3–SiO2 System, Journal of the European Ceramic Society, 26, 2285–2292, 2006.
[73] Agné, T., Sanitary Ware with Easy Cleaning and/or Antibacterial Properties, Tenside Surfactants Detergents, 44 (4), 222–225, 2007.
[74] Tulyaganov, D. U., Agathoupoulos, S., Fernandez, H. R., Ferreira, J. M. F., The Influence of Incorporation ZnO–Containing Glazes on the Properties of Hard Porcelains, Journal of the European Ceramic Society, 27, 1665–1670, 2007.
[75] Määttä, J., Piispanen, M., Kuisma R., Kıymäläinen, H.–R., Uusi–Rauva, A., Hurme, K.–R., Areva, S., Sjöberg, A.–M., Hupa, L., Effects of Coating on Clenability of Glazed Surfaces, Journal of the European Ceramic Society, 27, 4555–4560, 2007.
[76] Määttä, J., Piispanen, M., Kıymäläinen, H.–R., Uusi–Rauva, A., Hurme, K.–R., Areva, S., Sjöberg, A.–M., Hupa, L., Effects of UV–Radiation on the Cleanability of TitaniumDioxide Glazed Ceramic Tiles, Journal of the European Ceramic Society, 27, 4569–4574, 2007.
[77] Kuisma R., Fröberg, L., Kıymäläinen, H.–R., Uusi–Rauva, Pesonen–Leinonen, E., Piispanen, M., Melamines, P., Hautala, M., Sjöberg, A.–M., Hupa, L., Microstructure and Cleanability of Uncoated and Fluoropolymer, Zirconia and Titania Coated Ceramic Glazed Surfaces, Journal of the European Ceramic Society, 27, 101–108, 2007.
[78] Kronberg, T., Ritschkoff, A.–C., Mahlberg, R., Mannila, J., Kallio, M., Vesa, A., Hupa, L., Soil–Resistant Surfaces for Traditional Ceramics, Journal of the European Ceramic Society, 27, 1775–1780, 2007.
[79] Berto, A. M., Ceramic Tiles: Above and Beyond Traditional Applications, Journal of the European Ceramic Society, 27, 1607–1613, 2007.
[80] Sun, S. Q., Sun, B., Zhang, W., and Wang, D., Preparation and Antibacterial Activity of Ag–TiO2 Composite Film by Liquid Phase Deposition (LPD) Method, Bulletin of Materials Science, 31(1), 61–66, 2008.
[81] Marcos, P. S., Marto, J., Trindade, T., Labrincha, J. A., Screen–Printing of TiO2 Photocatalytic Layers on Glazed Ceramic Tiles, Journal of Photochemistry and Photobiology A: Chemistry, 197, 125–131, 2008.
[82] Pekkan, K. K., Karasu, B., and Kucuk, A., Production and Industrial Adaptation of Fast Single Firing Wall Tile Opaque Glass–Ceramic Glazes Containing Borax Solid Wastes, Proceedings of the REWAS 2008 Global Symposium on Recycling, Waste Treatment and Clean Technology,Cancun, Mexico, 371–378, 2008.
[83] Rincón, R. J., Benet, M. P., Juárez, J., Cabezón, C., Pedra, J. M., Carda, J. B., Martínez, J., Development of Glass–Ceramic Glazes with Anti–Slip Properties for Porcelain Tiles, Proceeding of Qualicer’08, Castellón, Spain, 329–343, 2008.
[84] Pekkan, K., Karasu, B., Production of Opaque Frits with Low ZrO2 and ZnO Contents and Their Industrial Uses for Fast Single–Fired Wall Tile Glazes, Journal of Materials Science, 44, 10, 2533–2540, 2009.
[85] Fortuna, M. D., Martini, E., Antibacterial and Self–Cleaning Ceramic Glazes, Ceramic World Review, 80, 44–46, 2009.
[86] Teixeira, S., Bernardin, A. M., Development of TiO2White Glazes for Ceramic Tiles, Dyes and Pigments, 80, 292–296, 2009.
[87] Cannillo, V., Esposito, L., Rambaldi, E., Sola, A., Tucci, A., Microstructural and Mechanical Changes by Chemical Ageing of Glazed Ceramic Surfaces, Journal of the European Ceramic Society, 29, 1561–1569, 2009.
[88] Piispanen, M., Määttä, J., Areva, S., Sjöberg, A.–M., Hupa, M., Hupa, L., Chemical Resistance and Cleaning Properties of Coated Glaze Surfaces, Journal of the European Ceramic Society, 29, 1855–1860, 2009.
[89] Pekkan, K., Karasu, B., Evaluation of Borax Solid Wastes in Production of Frits Suitable for Fast Single–Fired Wall Tile Opaque Glass–Ceramic Glazes, Bull. Mater. Sci., 33 (2), 135–144, 2010.
[90] Yoshida, H., Abe, H., Taguri, T., Ohashi, F., Fujino, S., and Kajiwara, T., Antimicrobial Effect of Porcelain Glaze with Silver–Clay Antimicrobial Agent, Journal of the Ceramic Society of Japan, 118 (1379), 571–574, 2010.
[91] Zeng, Z., Peng, C., Hong, Y., Lu, Y., and Wu, J., Fabrication of aPhotocatalytic Ceramic by Doping Si–, P–, and Zr–Modified TiO2 Nanopowders in Glaze, Journal of the American Ceramic Society, 93 (10), 2948–2951, 2010.
[92] Piispanen, M., Kronberg, T., Areva, S., Pimenoff, J., and Hupa, L., Easy–to–Clean Coatings on Glass and Glazed Surfaces, In Advances in Science and Technology, 66, 150–155, 2010.
[93] Sánchez, E., García–Ten, J., Sanz, V., Moreno, A., Porcelain Tile: Almost 30 Years of Steady Scientific–Technological Evolution, Ceramics International, 36, 831–845, 2010.
[94] Melchiades, F. G., Rego, B. T., Higa, S. M., Alves, H. J., Boschi, A. O., Factors Affecting Glaze Transparency of Ceramic Tiles Manufactured by the Single Firing Technique, Journal of the European Ceramic Society, 30, 2443–2449, 2010.
[95] Kaya, G., Karasu, B., and Cakir, A., Characterization of Diopside–Based Glass–Ceramic Porcelain Tile Glazes Containing Borax Solid Wastes, Journal of Ceramic Processing Research, 12 (2), 135–139, 2011.
[96] Hofer, M., Penner, D., Thermally Stable and Photocatalytically Active Titania for Ceramic Surfaces, Journal of the European Ceramic Society, 31, 2887–2896, 2011.
[97] Yeşilay, S. K., Karasu, B., Process Parameters Determination of Phosphorescent Pigment Added, Frit–Based Wall Tiles Vetrosa Decorations, Ceramics International, 38 (4), 2757–2766, 2012.
[98] Yeşilay, S. K., and Karasu, B., Glass and Ceramics with Phosphorescent Ability, Ceramics Technical, 34, 94–99, 2012.
[99] Gürbüz, M., Solaş, A., Küçük, A., Göktaş, A., and Doğan, A., Production of Environmentally Friendly Photocatalytic and Antimicrobial Ceramic Materials with Nanotechnology, Afyon Kocatepe University, Journal of Science and Engineering Sciences, 9 (3), 217–221, 2012 (in Turkish).
[100] Baheiraei, N., Moztarzadeh, F., and Hedayati, M., Preparation and Antibacterial Activity of Ag/SiO2 Thin Film on Glazed Ceramic Tiles by Sol–Gel Method,Ceramics International, 38(4), 2921–2925, 2012.
[101] Raimondo, M., Zanelli, C., Guarini, G., Dondi, M., Marani, F., Fossa, L., Photocatalytic Ceramic Tiles: Key Factors in Industrial Scale–up (and the Open Question of Performance), Qualicer’12 Proceedings, Castellón, Spain, 1–14, 2012.
[102] Petrovič, V., Ducman, V., and Škapin, S. D., Determination of the Photocatalytic Efficiency of TiO2 Coatings on Ceramic Tiles by Monitoring the Photodegradation of Organic Dyes, Ceramics International, 38 (2), 1611–1616, 2012.
[103] Partyka, J., and Lis, J., Chemical Corrosion of Sanitary Glazes of Variable Grain Size Composition in Acid and Basic Aqueous Solution Media, Ceramics International, 38 (1), 553–560, 2012.
[104] Agrawal, S., Tiwari, G. N., Pandey, H. D., Indoor Experimental Analysis of Glazed Hybrid Photovoltaic Thermal Tiles Air Collector Connected in Series, Energy and Buildings, 53, 145–151, 2012.
[105] Casasola, R., Rincón, J.Ma., Romero, M.,Glass–Ceramics Glazes for Ceramic Tiles–A Review Journal of Material Science, 47, 553–582, 2012.
[106] de Niederhausern, S., Bondi, M., and Bondioli, F., Self–Cleaning and Antibacteric Ceramic Tile Surface, International Journal of Applied Ceramic Technology, 10(6), 949–956, 2013.
[107] Pina–Zapardiel, R., Esteban–Cubillo, A., Bartolomé, J. F., Pecharromán, C., Moya, J. S., High Wear Resistance White Ceramic Glaze Containing Needle Like Zircon Single Crystals by the Addition of Sepiolite n–ZrO2, Journal of the European Ceramic Society, 33, 3379–3385, 2013.
[108]Murugan, K., Subasri, R., Rao,T. N. Gandhi, A. S., Murty, B. S., Synthesis, Characterization and Demonstration of Self–Cleaning TiO2 Coatings on Glass and Glazed Ceramic Tiles, Progress in Organic Coatings, 76, 1756–1760, 2013.
[109] Zhang, P., Tian, J., Xu, R., Ma, G., Hydrophilicity, Photocatalytic Activity and Stability of Tetraethyl Orthosilicate Modified TiO2 Film on Glazed Ceramic Surface, Applied Surface Science, 266, 141–147, 2013.
[110] Ghosh, S., Pal, K. S., Dandapat N., Ghosh, J., Datta, S., Glass–Ceramic Glazes for Future Generation Floor Tiles, Journal of the European Ceramic Society, 33, 935–942, 2013.
[111] Cacciotti, I., Nanni, F., Campaniello, V., Lamastra, F. R., Development of aTransparent Hydrorepellent Modified SiO2 Coatings for Glazed Sanitarywares, Materials Chemistry and Physics, 146, 240–252, 2014.
[112] Ke, S., Cheng, X., Wang, Q., Wang, Y., Pan, Z., Preparation of aPhotocatalytic TiO2/ZnTiO3 Coating on Glazed Ceramic Tiles, Ceramics International, 40, 8891–8895, 2014.
[113] Ghosh, S., Pal, K. S., Mandal, A. K., Biswas, N., Bhattacharya, M., Bandyopadhyay, P., Cordierite Based Glass–Ceramic Glazed Floor Tiles by Microwave Processing, Materials Characterization, 95, 192–200, 2014.
[114] Pekkan, K., The Thermal and Microstructural Behavior of a R2O–RO–(ZnO)–Al2O3–(TiO2)–SiO2 Based Macro–Crystalline Raw Glaze System, Ceramics International, 41, 7881–7889, 2015.
[115] Tezza, V. B., Scarpato, M., Oliveira, L. F. S., Bernardin, A. M., Effect of Firing Temperature on the Photocatalytic Activity of Anatase Ceramic Glazes, Powder Technology, 276, 60–65, 2015.
[116] Ferrari, C., Muscio, A., Siligardi, C., Manfredini, T., Design of aCool Color Glaze for Solar Reflective Tile Application, Ceramics International, 41, 11106–11116, 2015.
[117] Mohd, K., Hasmaliza, M., Effect of Rutile on Modulus of Rupture in Ceramic Glaze, Procedia Chemistry, 19, 10–14, 2016.
[118] Ferrari, C., Muscio, A., Siligardi C., Development of aSolar–Reflective Ceramic Tile Ready for Industrialization, Procedia Engineering, 169, 400–407, 2016.
[119] Hasmaliza, M., Foo, H. S. and Mohd, K., Anatase as Antibacterial Material in Ceramic Tiles, Procedia Chemistry, 19, 828–834, 2016.
[120] Knies, F., Schrantz, K., Aneziris, C., Gauckler, L., and Graule, T., Superhydrophilic Ceramic Glazes for Sanitaryware, Journal of Ceramic Science and Technology, 7 (1), 53–63, 2016.
[121] Gün, Y., Taşçı, E., Pekkan, K., and Karasu, B., The Effect of Different Commercial Frits on Phosphorescence Radiation in Varying Temperature Ranges, International Refereed Journal of Engineering and Science, (10), 42–58, 2017 (in Turkish).
[122] Karasu, B., Çakı, M., Utilisation of Phosphorescent Pigments Prepared by Dry Mixing and Solid State Sintering Method on Glazes for White Earthenware Body, Proceeding Book of the XI. International Eskisehir Terracotta Symposium, 337–356, 2017.
[123] Taşçi, E., Pekkan, K., Ispalarlı, M., Karasu, B., Development of Phosphorescent Violet/Purple Glazes on Traditional Glazed Tiles, Proceeding Book of the XI. International Eskisehir Terracotta Symposium, 695–709, 2017.
[124] da Silva, A. L., Dondi, M., and Hotza, D., Self–Cleaning Ceramic Tiles Coated with Nb2O5–Doped–TiO2 Nanoparticles, Ceramics International, 43 (15), 11986–11991, 2017.
[125] Fraga, D., Lyubenova, T. S., Martí, R., Calvet, I., Barrachina, E., Carda, J. B., Effect of Alkali Doping on CIGS Photovoltaic Ceramic Tiles, Solar Energy, 147, 1–7, 2017.
[126] Li, Z., Zhao, M., Zeng, J., Peng, C., Wu, J., High–Solar–Reflectance Building Ceramic Tiles Based on Titanite (CaTiSiO5) Glaze, Solar Energy, 153, 623–627, 2017.
[127] Gajek, M., Partyka, J., Rapacz–Kmita, A., Gasek, K., Development of Anorthite Based White Porcelain Glaze without ZrSiO4 Content, Ceramics International, 43 1703–1709, 2017.
[128] Tarhan, B., Tarhan, M., Aydin, T., Reusing Sanitaryware Waste Products in Glazed Porcelain Tile Production, Ceramics International, 43, 3107–3112, 2017.
[129] Gajek, M., Partyka, J., Leśniak, M., Rapacz–Kmita, A., Wójcik, L., Gahnite White Colour Glazes in ZnO–R2O–RO–Al2O3–SiO2 System, Ceramics International, 44, 15845–15850, 2018.
[130] Barrachina, E., Esquinas, M., Llop, J., Notari, M. D., Carda, J. B., Development of aGlass–Ceramic Glaze Formulated from Industrial Residues to Improve the Mechanical Properties of the Porcelain Stoneware Tiles, Materials Letters, 220, 226–228, 2018.
[131] Li, R., Lv, M., Cai, J., Guan, K., He, F., Li, W., Peng, C., Rao, P., Wu, J., Development of Sapphirine Opaque Glazes for Ceramic Tiles, Journal of the European Ceramic Society, 38, 5632–5636, 2018.
[132] Cai, J., Lv, M., Guan, K., Sun, Q., Peng, C., Wu, J., Liu, Y., Development of Spinel Opaque Glazes for Ceramic Tiles, Journal of the European Ceramic Society, 38, 297–302, 2018.
[133] da Silva, A. L., Dondi, M., Raimondo, M., Dachamir Hotza, D., Photocatalytic Ceramic Tiles: Challenges and Technological Solutions, Journal of the European Ceramic Society, 38, 1002–1017, 2018.
[134] Barmeh, A., Nilforoushan, M. R., Otroj, S., Wetting, and Photocatalytic Properties of Ni–doped TiO2 Coating on Glazed Ceramic Tiles under Visible Light, Thin Solid Films, 666, 137–142, 2018.
[135] Terjék, A., Dudás, A., Ceramic Floor Slipperiness Classification–A New Approach for Assessing Slip Resistance of Ceramic Tiles, Construction and Building Materials, 164, 809–819, 2018.
[136] Reinosa, J. J., Rojo, M. M., Del Campo, A., Martín–González, M., and Fernández, J. F., Highly Efficient Antimicrobial Ceramics Based on Electrically Charged Interfaces, ACS Applied Materials & Interfaces, 11 (42), 39254–39262, 2019.
[137] Barmeh, A., Nilforoushan, M. R., and Otroj, S., Photocatalytic and Self–Cleaning Properties of Glazed Ceramic Tiles Coated with TiO2 and Al–Doped TiO2 Thin Films, Journal of the Australian Ceramic Society, 55 (4), 1091–1097, 2019.
[138] Selli, N. T., and Yağyemez, T., Coating Solution with High Photocatalytic Activity on Ceramic Surfaces at Low Temperature, Journal of the Australian Ceramic Society, 56 (1), 59–66, 2020.
[139]http://vitra.com.tr/App_Assets/Catalogs/Clean-teknik-brosur.pdf (date accessed: 21.05.2020).
[140] http://www.erlus.de/TopiceSelf-cleaning/ (date accessed: 24.05.2020).
[141] Topateş, G., Alıcı, B., Tarhan, B., and Tarhan, M., The Effect of Zircon Particle Size on the Surface Properties of Sanitaryware Glaze, Materials Research Express, 7(1), 015203, 2020.
[142] Kronberg, T., and Hupa, L., The Impact of Wollastonite and Dolomite on Chemical Durability of Matte Fast–Fired Raw Glazes, Journal of the European Ceramic Society, 40 (8), 3327–3337, 2020.
[143] Wang, S., Li, X., Wang, Y., and Wu, J. Corrosion Resistance and Cleanability of Glazed Surface, International Journal of Applied Ceramic Technology, 1–27, 2020.
[144] Kunduracı, N., Öztürk, Z. B., and Binal, G., Energy Saving Surfaces with Phosphorescent Pigmented Vitrified Glazes, International Journal of Engineering Research and Development, 12(1), 118–124, 2020 (in Turkish).
[145] Nieves, L. J. J., Lot, A. V., Melchiades, F. G., Boshi, A. O., Digital Decoration for Ceramic Tiles: The Effect of Glazes Particle Size Distribution on the Inkjet Decoration, Boletin de la Sociedad Española de Cerámica y Vidrio, 59, 44–48, 2020.
[146] Amorós, J. L., Blasco, E., Moreno, A., Marín, N., Feliu, C., Sinter–Crystallisation Kinetics of a SiO2–Al2O3–CaO–MgO–SrO Glass–Ceramic Glaze, Journal of Non–Crystalline Solids, 532, 119900, 2020.
Comentários